Taking care of your mill drill machine includes following standard mill drill operating procedures as well as routine and scheduled maintenance. Following these simple mill drill care and maintenance guidelines will increase the life of your mill drill machine and improve the quality of your work.
Table of Contents
What are the types of mill drill machine care & maintenance?
Whether you have an advanced CNC milling machine like the one in the picture above or a more portable benchtop manual mill drill like the Rong Fu RF-25 (below), all mill drill machines require different types of care and maintenance to maintain performance within tolerances and give you the best results.
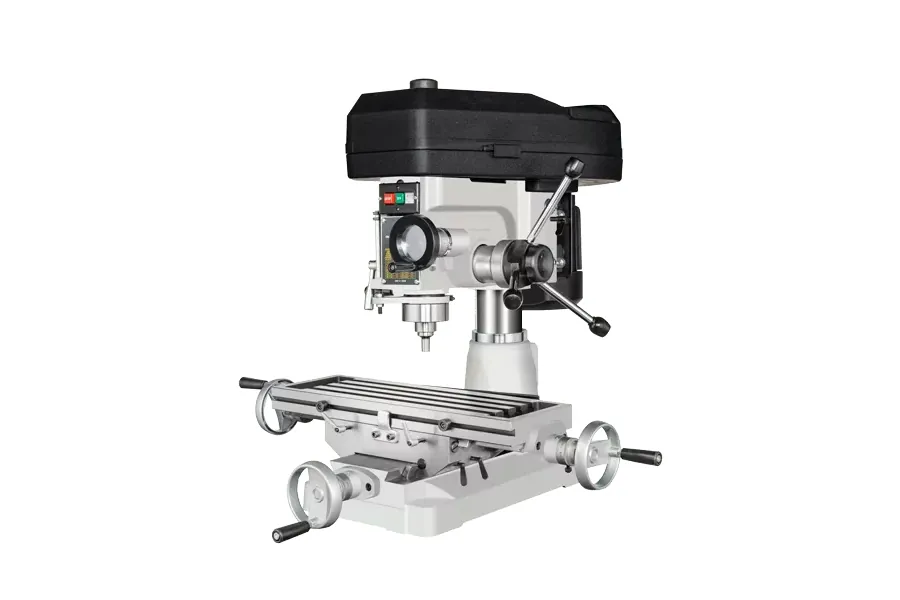
There are three types of mill drill machine care and maintenance that contribute to safe, efficient, high quality, cost-effective milling and drilling with your mill drill machine. If you follow these procedures from the very beginning, when you set up your mill drill machine for the first time, it will help you maintain consistent accuracy and performance and extend the service life of your mill drill.
- Daily mill drill maintenance
- In-service mill drill maintenance
- Scheduled mill drill servicing
Daily mill drill machine maintenance keeps your mill drill clean and serviceable and identifies any issues that need attention before they become problems. This includes a careful daily inspection for potential hazards and faults as well as routine cleaning and lubrication.
In-service maintenance tasks are mill drill care and maintenance operations that you consider before and after every single milling or drilling task. They contribute to the safety and longevity of your machine, cutting tools and accessories.
Scheduled mill drill servicing is a set of checks, calibrations and tests that should be performed according to your mill drill manufacturer’s maintenance schedule to maintain your machine in excellent condition, and includes checking and replacing service parts as they become worn during normal use.
Why is mill drill maintenance important?
Mill drill machine maintenance includes daily, in-use and periodic operations that should become part of your standard routine for four good reasons:
- Mill drill safety
- Efficient mill drill operation
- Quality of results
- Extended working life
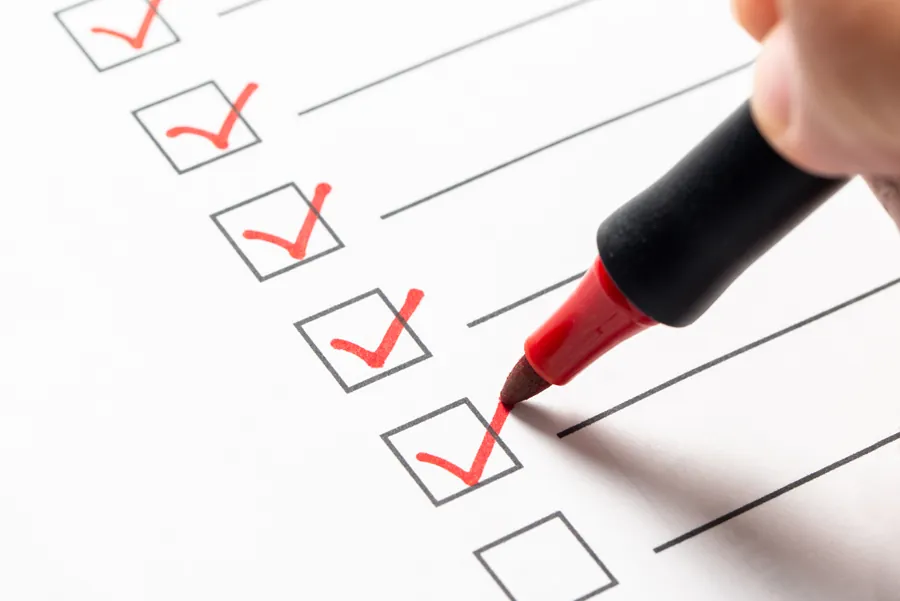
Daily Mill Drill Maintenance Checklist
This sequence of daily mill drill maintenance tasks should be carried out before starting work with your mill drill machine. Turn off the power to the mill drill machine before starting on this checklist, as a standard health and safety precaution. You will need to turn it back on towards the end of the maintenance program to verify safety cut-outs are working properly.
- Clean the mill drill machine exterior and remove debris from hard-to-reach areas with a brush and vacuum. Wash safety shields if visibility is obscured. Check the housing is free of rust, clean, treat and touch up paint if necessary.
- Clean table, clamp and guides and remove any burrs from the work surface.
- Check all control knobs, wheels, switches and levers for smooth, reliable operation.
- Check oil level in spindle gearbox (if applicable), check oil is clean, top up or change if necessary.
- Remove any burrs from the spindle cone.
- Inspect the spindle lowering and clamping mechanism of your mill drill machine, adjust for smooth, easy operation.
- Inspect the lubrication system, clean lubrication lines if debris is visible, ensure the lubricant reservoir is full and the oil sight window is clean.
- Inspection the cooling system of your mill drill machine: clean the cooling pump, filter, and coolant tank. Check coolant lines for leaks and replace if necessary. Top up the coolant tank to the fill line.
- Ensure power is turned off. Inspect the electrical system for fraying cables, burns or other indications of faults. Vacuum any dust outside the electrical and motor housings.
- Open the appliance cover, and check electrical connectors and components for looseness or damage. Vacuum any dust and wipe clean if necessary.
- Close all covers and turn on the power. Check if the limit switch is working properly, and if the door power-off safety function is working.
- Check the hydraulic system (if fitted) is functioning normally and there are no oil leaks.
- Ensure each control switch is functioning normally.
After your daily checks are complete, you’re ready to start work, but care and maintenance of your mill drill machine is a continuous process. Let’s now take a look at some good practices for in-service maintenance through the working day.
In-Service Mill Drill Maintenance
While using your mill drill there are some standard procedures and precautions that you need to follow to ensure safe, trouble-free operation, and reduce the risk of faults developing. Cleaning the table of swarf between cutting tasks is good practice, and you should always keep an eye on lubricant levels and top them up or investigate possible leaks if levels seem to be dropping faster than usual.
- Clean working area, table and clamps between cutting operations
- Check cutting tools for damage
- Maintain lubricant and coolant levels
- Make periodic checks for leaks
You should also check the condition of your cutting tools, as chips or damage are likely to damage your workpiece and can also cause damage to the spindle through vibration if it becomes unbalanced, as well as potentially becoming a hazard to the operator if fragments are chipped off the tool or workpiece.
Monitor and maintain the coolant system if your machine has one. Check coolant levels and filter condition regularly, and clean the tank and lines to maintain smooth flow and remove contaminants that can affect mill drill machining quality. A simple check around the machine for fluid leaks onto the floor should be part of your standard operating procedure.
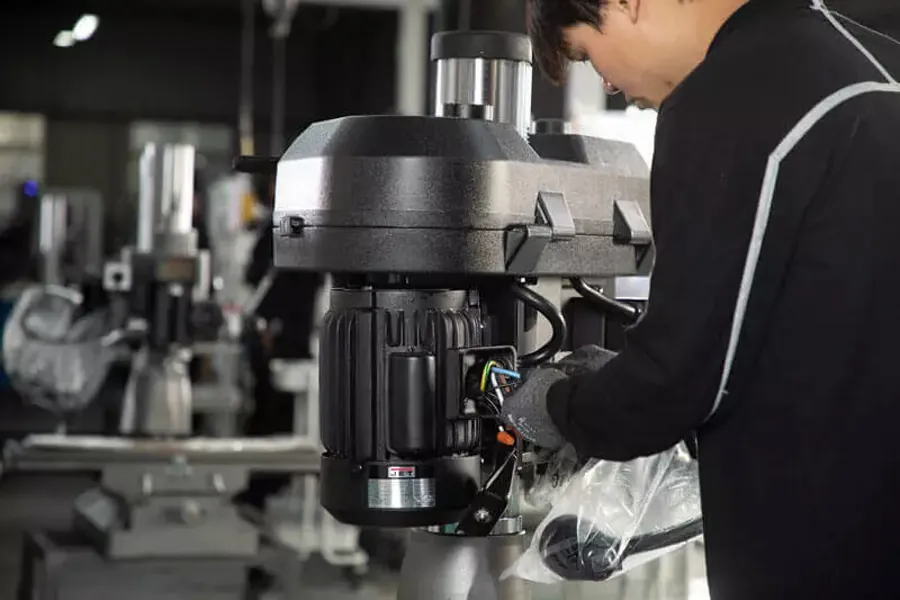
Scheduled Mill Drill Servicing
How frequently you should carry out a full maintenance service of your mill drill machine depends on how much use the machine gets. At a minimum, you should carry out a full service check every year, and if the machine is in daily use you should carry out checks on a monthly or even weekly basis.
Your mill drill machine operating instructions may give you guidance on when and how to carry out maintenance and servicing, but the following five point guide can be used to carry out routine servicing of almost all mill drill machines.
- Inspection & cleaning of your mill drill machine
Newer mill drills for 2025 may feature technological advances like electronic display panels and touch screens that must only be cleaned with the correct cleaning products to avoid damage, most other surfaces are lightly lubricated with machine oil. Refer to the manufacturer’s instructions for the correct procedures.
- Inspect and clean non-painted metal surfaces and lubricate lightly using a soft cloth soaked in light machine oil
- Inspect and clean all moving parts, check for smooth operation and lubricate using machine oil
- Follow manufacturer’s instructions for cleaning electronic displays and panels, using the appropriate cleaning system and materials
- During cleaning and oiling, check the machine for any wear or damage and note any faults that require correction before your mill drill can be put back into service
- Check brushes on mill drill motors if applicable
Remove and inspect any motor brushes (not applicable to brushless motors) for wear. Brushes should show even, smooth wear without grooves or burns. Replace both brushes when one is 50% worn, as a guide standard brushes are approximately 15mm in length, but check your machine specification.
- Check mill drill machine assembly supporting bolts are tight with no play
There are three locations where bolts commonly loosen over time on mill drill machines, pay additional attention to these and check your user manual for locations and procedures for tightening these bolts. These are the major moving assemblies of the mill drill machine and this is why they tend to develop slack or play over time.
- Column & Spindle Box
- Base & Saddle
- Saddle & Worktable
When servicing the saddle, removing it from the base enables thorough cleaning and lubrication of the assembly. When reassembling you should periodically check for smooth operation to ensure that you are carrying out the procedure correctly and all debris has been removed and the lubrication level is appropriate.
- Follow the correct sequence, clean, lubricate and apply specified torque when reassembling your mill drill
Locking screws, locknuts and adjusting screws may need to be loosened or backed off as part of the process. These procedures must be carried out in the correct sequence and to the specified torque. Cleaning debris and lubricating when checking play in these moving assemblies is an important part of the process to maintain precision and extend the life of components.
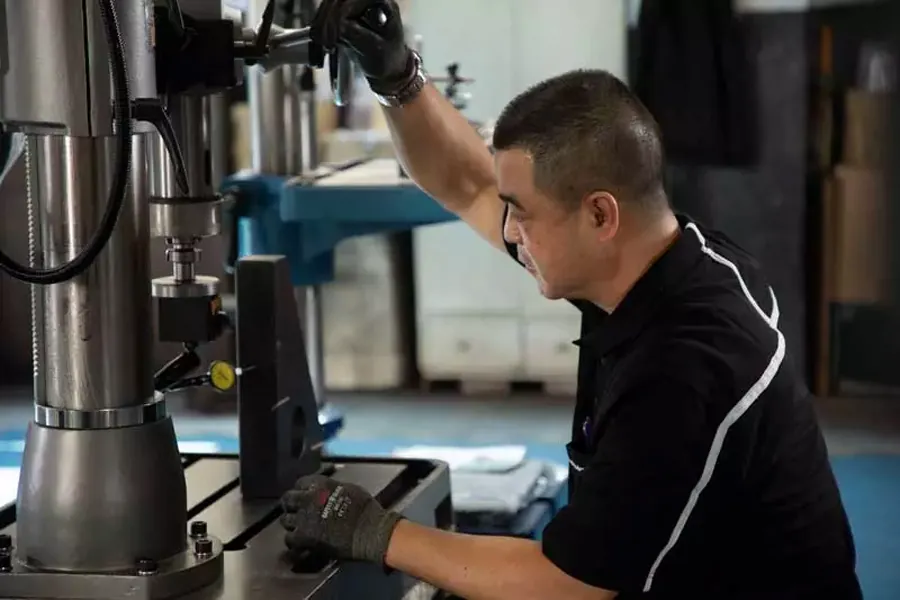
- Mill Drill calibration & accuracy
As part of regular servicing you need to make sure that the mill drill machine is properly calibrated and indexed and table, spindle and guides are aligned to maintain accuracy. Regularly check and adjust the machine’s alignment using precision measuring tools.
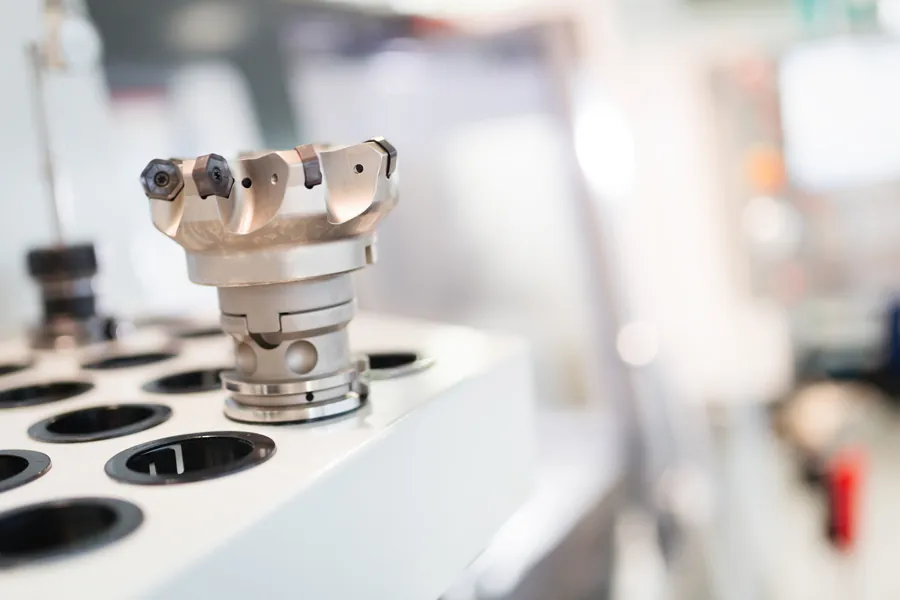
Mill drill cutting tool care & maintenance
Don’t forget, it’s not just your mill drill machine that needs care and maintenance, but milling cutters also need to be looked after. Chipped, burned, worn or broken tools will damage your workpiece and your mill drill. Because of the wide range of cutting tools you can use with your mill drill machine, this is not a subject we can cover in depth here, but just to remind you to inspect your cutting tools before every use.
Stop the machine immediately if there is any excess vibration, smoke or other signs of problems and rectify cutting tool faults and also check your mill drill machine for damage before restarting the machine and continuing your work with a new or repaired tool. Cutting tools with replaceable inserts are becoming increasingly popular, and if you use these it’s a good idea to keep a stock of spare inserts to maintain your workflow.
Rong Fu OEM mill drill machine care & maintenance
Our range of OEM mill drill machines is extensive, and manufactured to the highest quality standards following Toyota Production System (TPS) principles. We offer full documentation and support for OEM manufacturers to produce operation and maintenance manuals to help customers keep their machines operating at peak performance.
Contact us to discover how we can supply high quality OEM mill drill machines and help you integrate effective service and maintenance information into your customer support materials, manuals and services to meet the emerging demands of customers in 2025.