Implementing the TPS for metal cutting bandsaw manufacturing has delivered significant benefits to us and to our customers.
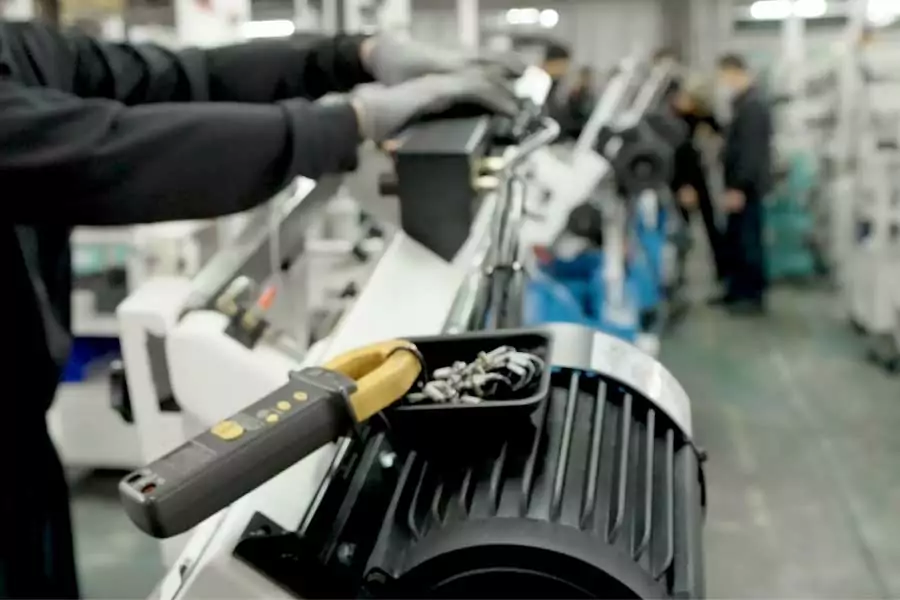
The Toyota Production System (TPS), and the Lean Manufacturing principles that it has inspired, were adopted by Rong Fu to manage our metal cutting bandsaw manufacturing systems. The TPS is a way of doing business developed by the Toyota Motor Corporation that focuses on maximizing customer value by eliminating waste and improving efficiency.
Table of Contents
What are the key benefits of applying the TPS to metal cutting bandsaw manufacturing?
Implementing the Toyota Production System in metal cutting bandsaw manufacturing has created many benefits for Rong Fu and our customers. These include waste reduction, continuous product improvement, standardized working practices, pull system demand implementation, empowering employees, continuous quality improvements, and better supply chain collaboration.
What are the 7 ways Rong Fu has successfully applied the TPS to metal cutting bandsaw manufacturing?
- Waste Reduction
- Pull System & Just-in-Time (JIT) Manufacturing
- Work Standardization
- Employee Empowerment & Employee Engagement
- Continuous Improvement Culture
- Enhanced Quality Management
- Improved Supply Chain Collaboration
Adopting TPS has increased our productivity, reduced metal cutting bandsaw manufacturing costs, increased customer satisfaction levels, and continues to build our competitive advantage in the metal cutting bandsaw market.
Waste Reduction
Waste reduction is a core feature of the TPS. Metal cutting bandsaw manufacturers can minimize cost impacts in five ways by identifying and eliminating material and efficiency waste:
- Not holding excess inventory
- Avoiding overproduction
- Reducing waiting times
- Stopping unnecessary movement of people and equipment
- Reducing the need for defect repairs
Implementing waste reduction in our metal cutting bandsaw manufacturing has delivered three significant benefits:
- improving efficiency
- reducing costs
- increasing productivity
Pull System & Just-in-Time (JIT) Manufacturing
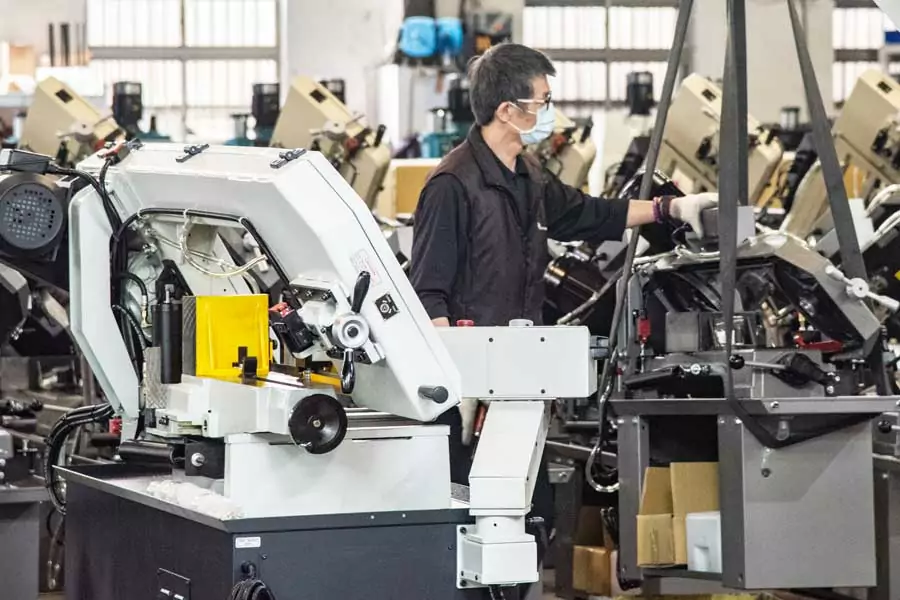
Pull System and Just-in-Time (JIT) production describes a production process where materials and components are only restocked when they are needed to enable current production demand. New products are manufactured ‘just in time’ to deliver to customers rather than being supplied from stock.
Production driven by market pull means you only manufacture metal cutting bandsaws to meet customer demand. This reduces the requirement for storage space and the cost of having finance locked away in unsold products. Because you do not keep excess inventory in stock, it is also much easier to adapt designs and increase innovation to match customer demand.
Metal cutting bandsaw manufacturers can improve efficiency and minimize costs in three ways by adopting pull system and JIT methods:
- Reduce the cost of unused inventory
- Shorter lead times for manufacturing
- Quicker response to changes in customer demand
Work Standardization
The principle of standardized work is another key TPS approach. Standardized work means learning the best way to carry out a task and then having procedures in place to ensure that the task is always done the same way.
Standardizing work procedures in metal cutting bandsaw manufacturing has enabled Rong Fu to reduce variation in production processes, increase quality standards, make high quality standards easier to monitor and achieve, and also set up systems for continuous improvement in work procedures.
Employee Empowerment & Employee Engagement
The TPS supports empowering employees and including them in decision-making processes. Employee engagement and generating opportunities for employee learning and growth help build a motivated, positive workforce, and a working environment that benefits from expert employee feedback.
At Rong Fu we have found that empowering our employees and engaging them in the evaluation and improvement of our metal cutting bandsaw manufacturing has led to increased innovation, rapid problem-solving, and general benefits to organizational performance.
Continuous Improvement Culture
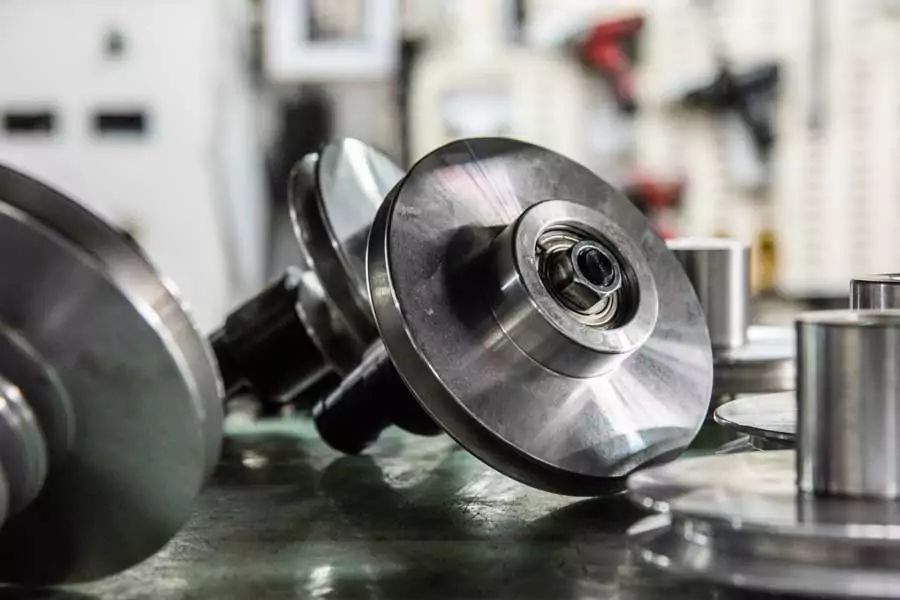
The culture of continuous improvement is central to the TPS. At Rong Fu we involve every employee in finding ways to improve tasks and processes. We have discovered that metal cutting bandsaw manufacturing benefits from continuously identifying and implementing incremental improvements to our production systems.
We have experienced three significant changes in our metal cutting bandsaw manufacturing business as a result of adopting continuous improvement culture:
- enhanced quality
- increased throughput
- reduced lead times
Enhanced Quality Management
There are many quality control methodologies that are part of the TPS approach, and are easily applied to metal cutting bandsaw manufacturing. Root cause analysis and mistake-proofing are two techniques that we have found very effective for continuous quality improvement.
A basic principle is to focus on quality at the source. This is why it is important to implement robust quality control processes. We have discovered that a metal cutting bandsaw manufacturer can achieve three important quality goals by following this process:
- Reduce defects
- Improve product reliability
- Enhance customer satisfaction
Improving Supply Chain Collaboration
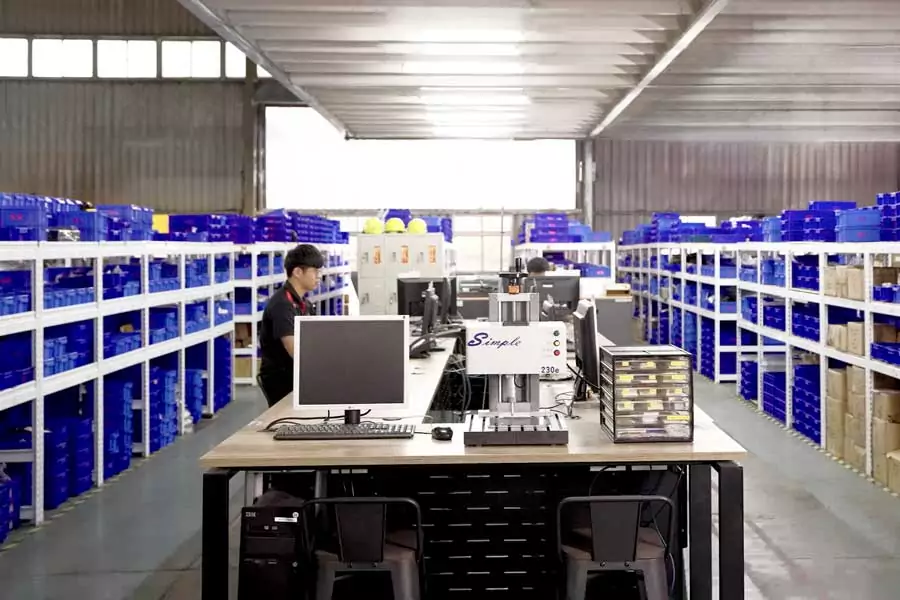
As part of the commitment to lean manufacturing on just-in-time principles, driven by customer demand, supply chain systems make a significant contribution to the success or failure of TPS style metal cutting bandsaw manufacturing.
The smooth flow of ordering, accounting, and feedback information to enable timely supply of high quality raw and processed materials depends on close collaboration and effective communication with suppliers
We have established strong relationships with our suppliers and continue to implement and refine efficient supply chain practices like supplier Kanban systems. This has enabled us to make gains in three supply chain related processes:
- Reduction in lead times
- Better supply chain management
- Faster response to customer demands
Metal Cutting Bandsaws For 2023
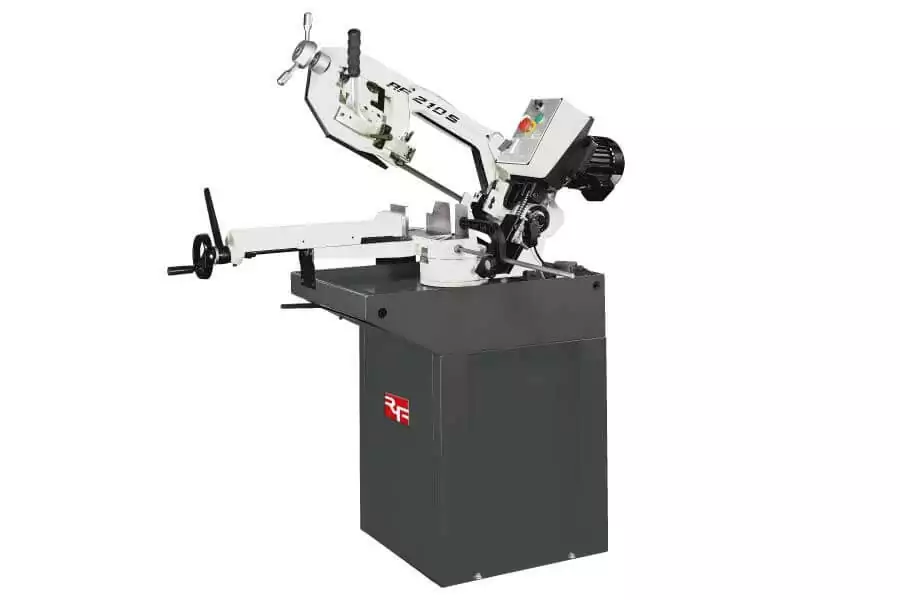
The Rong Fu RF210 pictured above is a modern metal cutting bandsaw, one of the wide range of metal cutting bandsaws we manufacture at our factory in Taiwan. Rong Fu metal cutting bandsaws have standard cutting capacities between 4” and 20” and can be customized with a range of options for any customer requirement.
12 Optional Features to Customize Your Rong Fu Metal Cutting Bandsaw
- Cost-Saving DC Variable Speed Motors
- 3-Phase Metal Cutting Band Saws
- Gearhead or Belt Drive (three stage)
- Portable, Bench or Floor Mounting
- Tru-lock Vise
- Semi Auto Saw Bow Lifting
- Vertical, Horizontal or Variable Blade Alignment
- Hydraulic Downfeed Control
- Coolant Systems for Wet Cutting
- One Way or Two Way Swivel
- Quick Change Systems for Horizontal to Vertical Cutting
- Semi Auto Hydraulic Vise
The complexity of modern metal cutting bandsaws requires attention to detail and excellence in production processes to guarantee the high quality, dependable results that our customers demand. Adopting the TPS has helped us to keep ahead of the competition and offer highly cost effective products to respond to the challenging market conditions we are seeing in 2023.
Contact us to discover why so many global brands choose Rong Fu metal cutting bandsaws. All our metal cutting bandsaws are built to the highest quality control standards, manufactured with care by our dedicated engineers, and are equipped with many highly attractive features as standard options.