We previously looked at choosing a metal cutting bandsaw blade, installing & adjusting blades, and breaking them in. Now let’s discuss the features of bimetal bandsaw blades and carbide tipped metal cutting bandsaw blades. We’ll compare their features and discuss how blade material can improve the efficiency and cost-effectiveness of your workshop metal cutting bandsaw.
Table of Contents
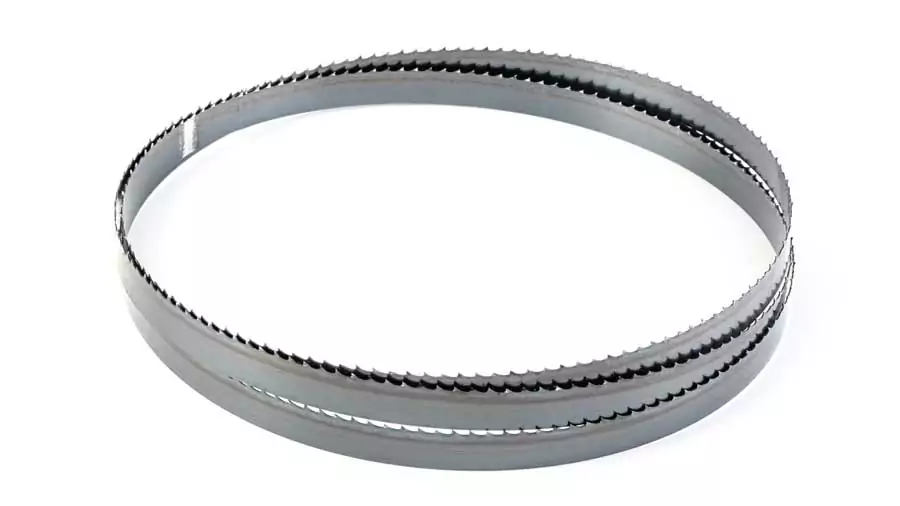
How important is blade material for metal cutting bandsaw blades?
Blade material is the second thing to decide after blade pitch (TPI). Deciding on blade pitch is the first stage in choosing a metal cutting bandsaw blade, because it depends on the thickness of materials being cut. After blade pitch, blade material is the most important consideration for selecting the right metal cutting bandsaw blade for any task. The only exception is for cutting extremely hard and toughened materials, which can only be cut with bi-metal or carbide tipped blades.
What are the 3 materials used for metal cutting bandsaw blades?
- Carbon steel
- Bi-metal
- Carbide tipped
Carbon Steel Metal Cutting Bandsaw Blades
Carbon steel, alloyed steel and mild steel blades are the most basic types of metal cutting bandsaw blades. These are good for general purpose cutting of softer materials, and are a very affordable option, especially if your metal cutting bandsaw is not in everyday use in your workshop.
These blades are made from strips of steel with the tooth profile cut into the edge. The ends are welded together to make bands to fit your metal cutting bandsaw. Steel can be hardened to different degrees during the manufacturing process, so you should still check the manufacturer specifications when purchasing a steel metal cutting bandsaw blade for general purpose use.
Bi-Metal Metal Cutting Bandsaw Blades
Bi-metal blades are more expensive than carbon steel but are more durable, provide a cleaner cut and a better finish. As a general purpose blade material that can cut almost any material, the bi-metal bandsaw blade is an industry standard for workshop use, especially if you need to cut high volumes of any but the softest materials.
Bi-metal metal cutting bandsaw blades feature a high-speed steel (HSS) hardened cutting edge welded to a more flexible steel band. Hardened steels tend to be brittle, so it is not possible to make an entirely HSS bandsaw blade as it would soon break from stress fractures caused by bending around the metal cutting bandsaw drive wheels. Welding a hard cutting edge onto a steel blade provides the hardness needed to cut through metal without compromising the flexibility and lifespan of the blade.
Carbide Tipped Metal Cutting Bandsaw Blades
Tungsten carbide tipped metal cutting bandsaw blades are the best choice for tough or abrasive materials. A problem with cutting very hard materials with a metal cutting bandsaw is that when the material is as hard or harder than the bandsaw blade it causes very rapid blade wear. Carbide tipped bandsaw blades have clear advantages over carbon and bi-metal blades for cutting hardened steels and exotic alloys.
Carbide tipped blades are similar to bi-metal blades, because the cutting teeth are brazed, or welded, to a softer, more flexible, steel band. The tungsten carbide teeth are extremely hard, and result in a very durable, long-lasting metal cutting bandsaw blade that is ideal for high volume production as well as cutting very hard materials.
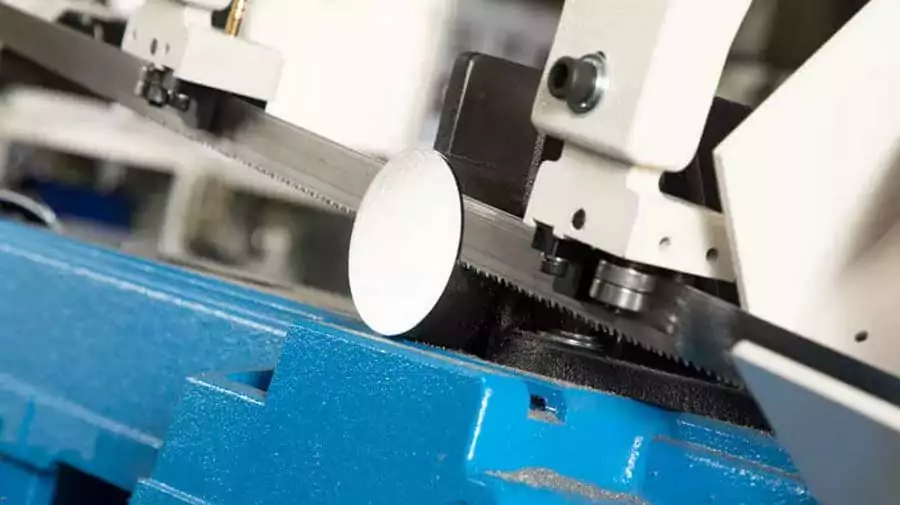
How do the different metal cutting bandsaw blade materials compare?
Blade material | Workpiece Suitability | Advantages | Disadvantages |
Carbon steel |
|
|
|
Bi-metal |
|
|
|
Carbide tipped |
|
|
|
Selecting the correct blade material
There are several factors to consider when choosing blade material, the most significant limitation is going to be if you need to cut very tough or hardened materials. If so, then you will need to use bi-metal or carbide tipped metal cutting bandsaw blades. This is partly because of the heat generated when cutting harder materials, and also this makes it essential to lubricate and cool the blade effectively during operation.
Compatibility chart of workpiece materials and blade materials
Material | Carbon Steel | Bi-Metal | Carbide Tipped |
Non-ferrous & mild steels | +++ | ++ | + |
Hardened steels & alloys | + | +++ | +++ |
Tough & exotic materials | – | + | +++ |
Softer materials can be cut very readily with a standard carbon steel blade, and you may get better results with less chipping and a better surface finish than you would with a more aggressive bi-metal or carbide-tipped blade. Another point to consider is that carbide teeth tend to be wider than steel teeth, which makes a wider kerf with more stress on the workpiece during cutting. Very thin materials may be distorted or damaged by cutting with a carbide tipped blade unless extreme care is taken with your setup.
Bi-metal blades are the preferred choice for frequent use in workshop metal cutting bandsaws. They offer a good all-round performance, with relatively clean cutting and are available in a variety of tooth sets and TPI, so you can keep a range of bi-metal blades in your inventory at a lower cost than using carbide blades and are more likely to find a bi-metal blade that is suitable for thinner materials or delicate cutting.
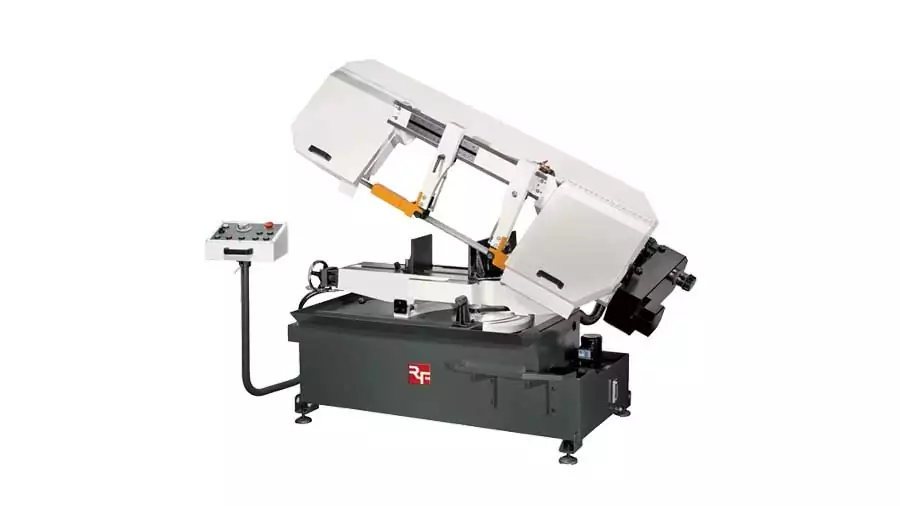
The Best Metal Cutting Bandsaws Give The Best Blade Performance
When selecting blade materials, it’s not going to help you if your metal cutting bandsaw is not suitable for the material type you need to cut with the blade you need to use. Remember that harder materials, bi-metal and carbide tipped blades all require excellent lubrication and cooling during operation to extend the life of these more expensive blades and avoid damage to the workpiece.
Another important issue with bi-metal and carbide tipped blades in particular is being able to set up the blade with high precision to avoid twisting and excessive stress on the blade during operation. The hardened edges of bi-metal blades may crack under strain and carbide teeth may detach if the blade does not run smoothly through the bandsaw and is not maintained in correct alignment during cutting.
At Rong Fu, we have more than 40 years of experience manufacturing and supplying high quality, precise, OEM metal cutting bandsaws to global brands who retail worldwide. If you are going to invest in high quality blades for high precision cutting operations, fitting them to a low quality bandsaw will reduce blade life and increase replacement and repair costs.
Matching your high performance blades to a high performance bandsaw with advanced blade tension, setup and lubrication will give you the best results. The Rong Fu 13” Semi Auto Metal Band Saw
RF-335 pictured above is a good example of a heavy duty workhorse that will make short, clean-cutting, work of the toughest jobs with the correct blade combination and fitting. Contact us to discover how the range of Rong Fu metal cutting bandsaws includes models to suit every blade type and cutting requirement.